Flexible automation is essential in a company’s strategy to diversify product manufacturing, increase quality, and reduce the direct labor content of a wide range of motors and generators. Over the years, Alliance Winding Equipment has worked with many clients who have reservations or face challenges that keep them from investigating and investing in product automation. In many cases, there are solutions to what they perceive as challenges or hurdles that keep them from moving forward with automation to improve their manufacturing process, deskill operations, and produce a higher quality product at higher outputs. In the following content, we will discuss some of the popular myths that we have been able to work through with our clients and help them move towards increased or full automation.
Motor Manufacturing Myth #1: “Our Product line is too diverse to justify new equipment.”
Many companies think they are unique in their complete range of winding specifications or stator/lamination designs. Today, this variety is more the norm than the exception. In most cases, gone are the days when lines were dedicated and only set up to run a single product designation. The new motor designs offer greater efficiency and material savings while the demand for legacy products remains. Alliance has a full line of semi-automated and automated machines that address the needs of small batch manufacturers.
- Equipment that can handle automatic stack changes with specification storage and model setup.
- Coil form changeover within one (1) minute for different winding patterns.
- Quickly change a complete frame size to a new lamination without hand tools.
- Advanced diagnostics to quickly identify system interruptions.
- The ease and availability of remote support with advanced diagnostics to support our equipment.
- Onboard maintenance scheduling to increase machine availability.
- Operator set-up manuals with a bill of materials that allow instant ordering of support parts.
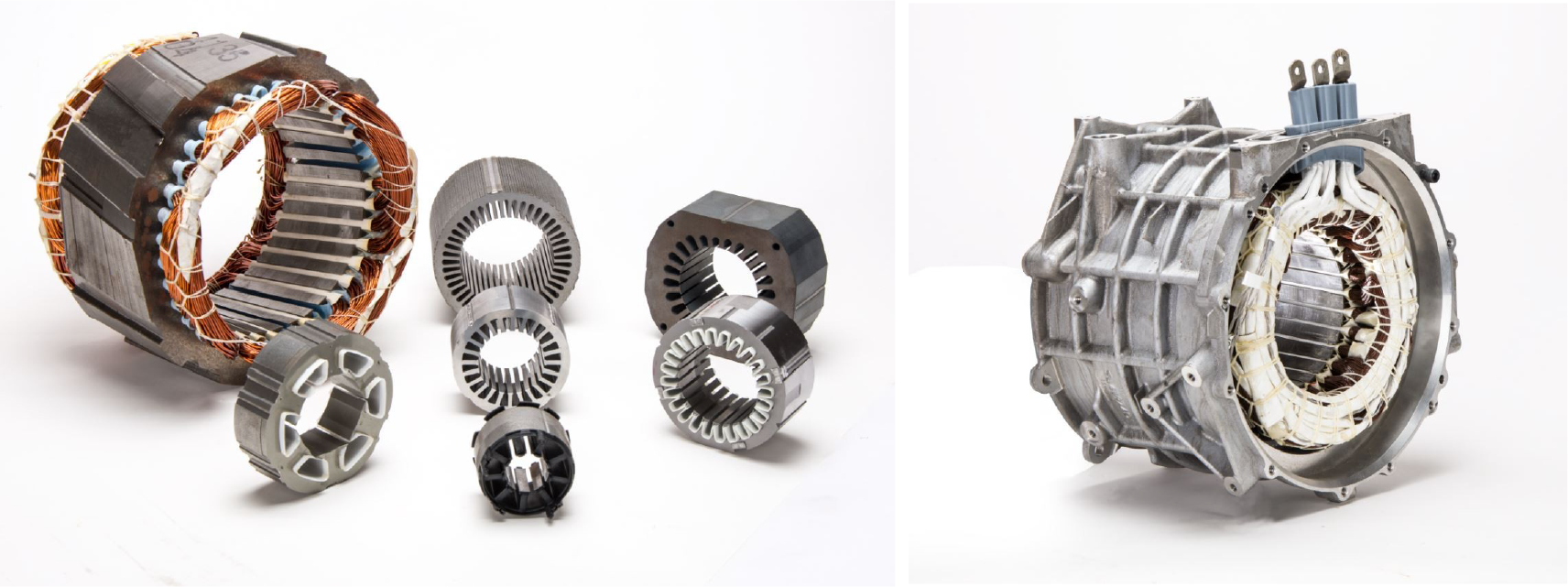
Motor Manufacturing Myth #2: “Moving production to lower-wage countries is more cost-effective.”
Many companies have moved or are evaluating moving their production lines and systems without considering certain hidden costs or the availability of automation to increase productivity. While this trend has increased over the years, many companies are still weighing their options with automation over relocation. Often, the additional cost of relocation is not recognized until it is too late. The following have been reported as unforeseen relocation costs and should be considered when making these investment decisions.
- Increased Training Cost: In many emerging economies, the factories experience high employee turnover, and in some emerging economies, the management and engineering staff turnover is the same. This requires the remainder of the supervision to train new, inexperienced workers continually. This can
- Increased Scrap: With inexperience comes scrap. Experience in the motor and generator business is invaluable. The cost of scrap can have a significant impact, and startup plants must be monitored to control the amount of scrap. In contrast, established plants with quality standards and proven experience can significantly monitor and maintain lower scrap levels.
- Increased Maintenance Costs: A frequently changing workforce results in an increase in mistakes and machine damage. The high cost of tooling and tooling dedicated to the product can significantly increase replacement tooling costs and cause significant delays in manufacturing when the equipment is down for an extended period due to replacement parts. Not only do these mistakes drive up the cost of operating a machine, but they also significantly reduce the utilization of the equipment.
- Indirect Labor: No matter the location, all facilities require an extensive staff of skilled technicians, engineers, and management to produce a quality product efficiently. Such a staff can be just as create issues in an industry that demands highly skilled labor to produce quality products as a significant investment in lower-wage locations. The cost can be substantial when considering the requirement for skilled employees' training and monitoring the unskilled employees.
Motor Manufacturing Myth #3: “We change over too much to be able to automate.”
It is no longer true that automation and flexibility are mutually exclusive. Driven by our customers’ need to manufacture a wide variety of motors with minimal direct labor, Alliance Winding Equipment has developed a range of Flexible Automation Systems that meet the needs of the modern manufacturer.
Small Frame Stator Assembly
Alliance small-frame flexible automation systems feature automatic stack height adjustment and model changeover in minutes. In addition, the systems can be tailored to your specific manufacturing requirements and required takt times. Based on these requirements, the number of operators can be increased or decreased depending on the level of automation. The Alliance systems also offer manual and automatic phase insulation placement options.
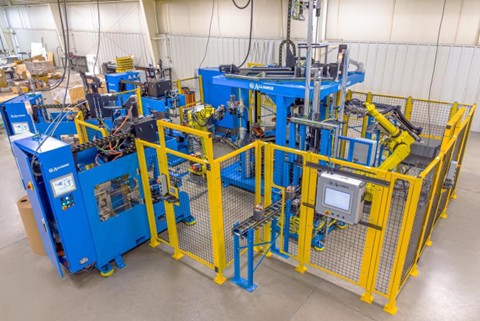
Medium Frame Stator Assembly
The Balanced Winding System (BWS) has a long history of success in the industry and can handle NEMA 140 to 400 frame sizes. The system has been successful due to its robustness, flexibility, and product quality. The BWS incorporates Winding, Wedge making, inserting, and Drift/Preforming into one automatic system that a single operator can monitor. The BWS is flexible and can be set up for multiple frame sizes. Three operators can change over the BWS stator assembly cell within 20-30 minutes without requiring hand tools. Dedicated tooling storage and lift assist devices have also been developed to help optimize the changeover process.
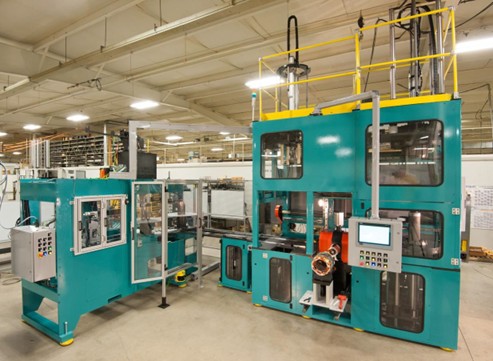
Large Frame Stator Assembly
Alliance can handle stator automation up to NEMA 440 Frame, including handling stack heights up to 22in (559mm). Systems include vertical and horizontal processing options to suit your manufacturing requirements best. Historically, large frame products in the NEMA 320 – 440 Frame sizes have been processed horizontally, which creates challenges for winding and insertion automation. Alliance has continually pushed the limitations of vertical winding and insertion for large frame stator automation and now offers complete vertical automation systems up to NEMA 440 Frame.
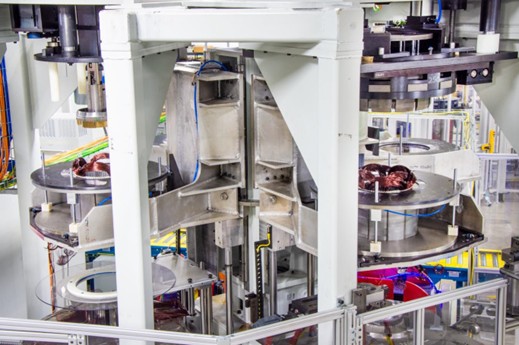
Alliance Winding Equipment, Joyal, and AWE Newtech have worldwide manufacturing operations with a global perspective on manufacturing and competitiveness. Alliance understands the demand for high-quality equipment and reliable service, regardless of location or where the production equipment is required. Emerging markets will still demand high-quality machines with the latest machine designs and automation. Automation and higher manufacturing productivity will lead to a subsequent wage increase for skilled technicians and operators. No matter where the economic pendulum swings and as the playing field levels, the high-quality motor and generator manufacturers globally positioned to their customer base with flexible automation to respond quickly will prosper.
Ready to Upgrade Your Electric Motor Manufacturing Process?
If you're interested in exploring how modern automation and advanced technologies can improve your manufacturing, contact us today to learn more about our cutting-edge solutions.